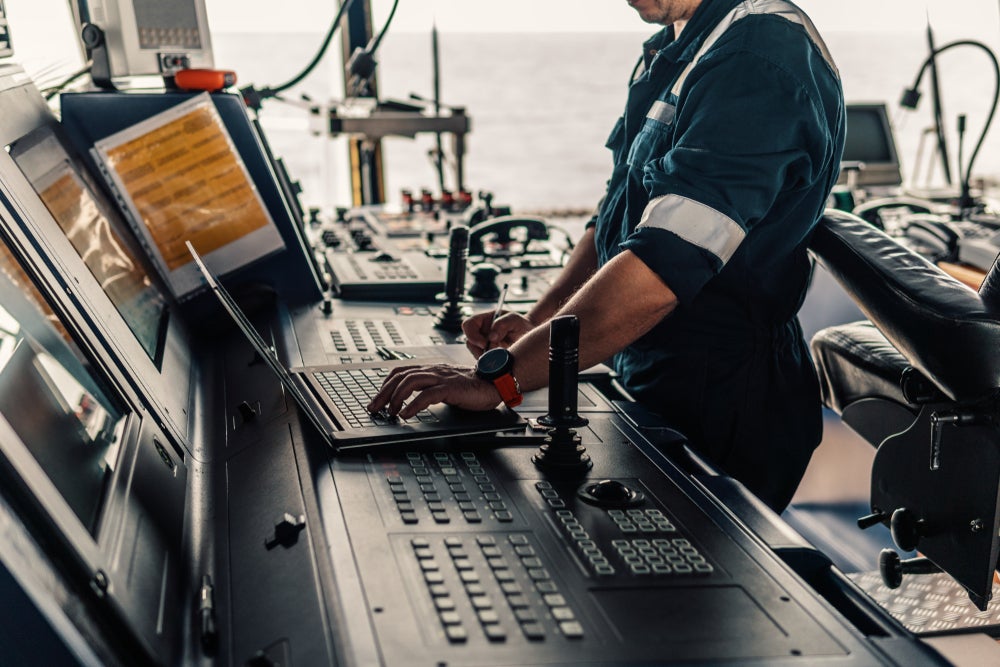
Ask a naval architect and they will tell you designing a ship consists of four phases – concept, preliminary, contract and detail – each running through the same “spiral” of requirements, including powering, arrangements, stability and costing. When this spiral was first developed in the 1950s, traversing it seemed like the most efficient way to get from a blueprint to a finished vessel. But the complexity of modern ship design means errors and logjams are increasingly common. Jan van Os is the vice president for marine industry strategy at Siemens Digital Industry Software and has over 30 years’ experience working with marine customers at every stage of the shipbuilding process. He gives his insights on how the industry has changed over the course of his career and how an integrated digital approach can bring ship design into the 21st century.
Could you provide some background on the origins of modern ship design – and why this may no longer be fit for purpose?
Jan van Os: The design spiral was and still is the basis of ship design: you start from scratch with a blank piece of paper, follow all the steps based on various assumptions and make sure those assumptions are getting better. But modern technology has brought with it novel requirements from ship owners and regulators. Meeting these complex requirements while coordinating all the different groups needed to fulfil them can hold up designs and cause costs to rise. One way to mitigate potential risks is by using the best marine design solutions, so everyone is using the same tools and working across domains on a comprehensive digital twin. Another way is by doing more simulations to connect dots in the design spiral, improving your basic assumptions about a design from the outset. Together these allow you to better control the design spiral. This is why we want to introduce integrated ship design and engineering.
Ship designers are under pressure to simultaneously reduce ships’ carbon footprints while ensuring they are equipped with the latest technology. How are digital innovations helping designers to face these challenges?
Jan van Os: Digital transformation is the only way to respond to the challenges presented by the complexity of the ships themselves and the drive toward sustainability. In the industry, the International Maritime Organisation is setting targets to reduce carbon emissions by 50% by 2040. The bigger companies, like Maersk, are setting even sharper targets, aiming for carbon neutrality by the same deadline. Working out how to do that is driving the industry. We need new fuels, new ship designs, new propulsion systems. And there’s increasing complexity to consider. Fossil fuels being used now will be replaced by methanol, hydrogen and liquefied natural gas, and the use of batteries for electric propulsion will increase. The speed of innovation can only be handled by digital transformation. A human can oversee a certain amount, but the scale of requirements and interactions at play means you need systems in place to control the many moving parts.
What hurdles are still standing in the way of simulation in the shipping industry?
Jan van Os: The shipping industry is conservative; it depends a lot on model testing and is cautious about adopting new analysis methods. Some shipyards are still sceptical about simulation, even though it’s becoming more popular. But we are seeing a big increase in demand for simulation. Model-based system engineering, for example, is getting more traction in marine, especially with naval shipbuilders starting to examine complete ship systems to make sure that designs fulfil the requirements. With our simulation capabilities, we can support that need for the marine industry.
How is Siemens helping ship designers who want to adapt to the evolving industry by trying new approaches, but are reticent about a completely digitalised, fully integrated transition?
Jan van Os: The shipbuilding industry knows it needs to change. Design teams are aware what they’re doing isn’t quite working and they’re looking for the way forward. And there’s so much concern around what the future of shipping looks like; they need a solution that’s going to work no matter what they end up building in 10-15 years. Some of them may have invested in point solutions to resolve one little bit of the design process, but what they haven’t got is an integrated, completely connected design solution, which gives you all those benefits and more – a comprehensive digital twin and a single source of truth for everyone working on a project.
What are the dangers of holding back on implementing integrated ship design?
Jan van Os: A department might go to another to ask for support, they put it on their list, but nothing is really connected. In a fast-moving project, this means some information might end up falling through the cracks. One team might tear ahead with the rest of the development while another is looking for stability or finding improvements. And that stability could be calculated with old information because they don’t know a revision has occurred. Data management is needed, allowing everyone to check in on the latest information and stopping valuable time being lost throughout the design and build process. Integration is key to doing this better and faster. Making a mistake in the beginning can have big consequences during the building – not just for delivery time but for budgets too.
Could you summarise three key benefits of integrated ship design?
Jan van Os: Rolling out a digital twin, not only in the design but in the whole manufacturing process, and beyond in services and operation. Orchestration across domains, using data in the right place and at the right time to ensure all teams have one source of truth and are moving together. And simulation-driven design, meaning different parts of the design spiral can be connected.
How can ship designers take steps now to safeguard against changes on the way in the coming years?
Jan van Os: Ship designers can step into the digital journey, putting data management and product lifecycle management systems in place to share information with their own departments and decision makers throughout the supply chain. The ship building industry will have to adapt to digitalisation both during building and after the ship is delivered: they are already going in the right direction, but they are not there yet. Without having an integrated solution where you start doing your engineering, you cannot support the building process. You need the right information to be brought to the floor in a 3D environment to make sure the right things are being done. Those who fail to do so will simply be passed by the competition and eventually disappear. It is happening faster than most shipyards are anticipating. They can’t afford to wait ten years; they need to act now.
What would be your one top tip for ship designers hoping to futureproof themselves against changes in the industry?
Jan van Os: Designers must embrace change. If they are not open to change, it is almost impossible to get digitalisation working. But if they are – use Siemens. We are a partner with our customers and want to help them on their digitalisation journey. With the right partner to provide support in that journey, you can stay on track through the ups and downs. Sometimes it’s hard, especially if you need to change engineers and key suppliers. But with the right partners, it is possible.
Further details:
To find out more about the benefits of integrated ship design and how working with Siemens Digital Industries Software can help, download the whitepaper below.