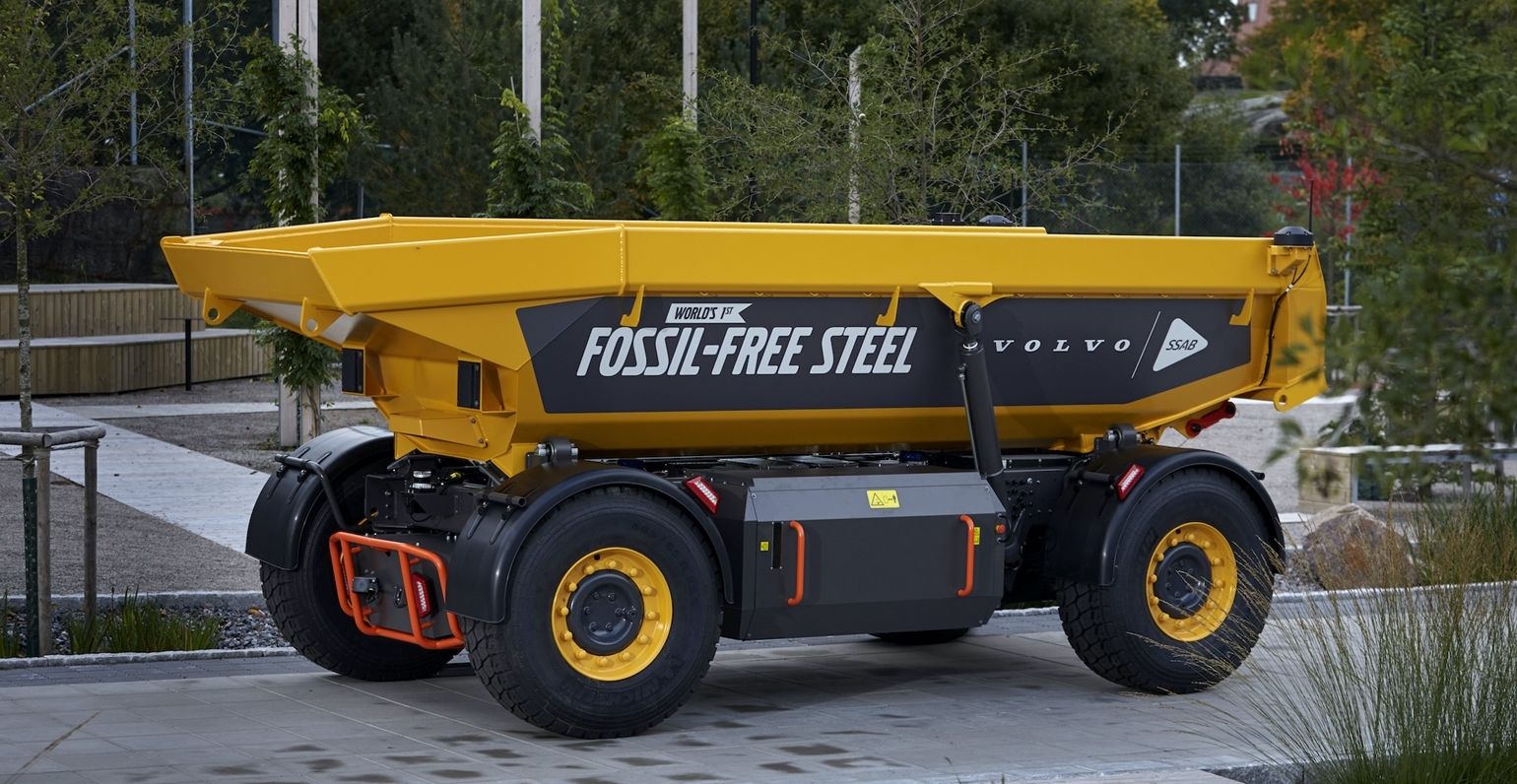
SSAB, in partnership with miner LKAB, and Swedish government-owned energy utility Vattenfall has been researching the viability of producing its high-quality steel products without emitting any greenhouse gases (GHGs).
Beginning in 2016, the group proposed to produce fossil-free steel in quantity by 2035.
The partnership was named ‘HYBRIT’ (Hydrogen Breakthrough Ironmaking Technology), and each company began working to ensure their material input to the experiment was going to be GHG-emissions neutral.
Iron ore is traditionally processed or ‘reduced’ by heating it to remove the oxygen that is present in the raw ore, so the challenge LKAB faced was to use a heat source for the reduction that did not emit any GHGs.
Testing times
Mining giant LKAB, whose operation based at Luleå, Sweden was the selected test partner responsible for producing fossil-free sponge iron. They started by researching how to make sponge iron (or DRI – Direct Reduced Iron), instead of conventional iron ore pellets, without using any GHG-releasing fuel. They tested replacing the usual coal and coke with biofuel, then moved on to plasma and hydrogen as heat sources to see which would be the most efficient in terms of the lowest, or no, GHG emissions.
Hydrogen was chosen as the fuel which LKAB moved forward with to ensure there were going to be zero GHG emissions from either the mine, the logistics or the processing plants when making sponge iron into HBIs (Hot Briquetted Iron).
A test plant was built in 2018, where they used their raw iron ore and hydrogen produced using fossil-free electricity (generated using wind power) by Swedish state-owned Vattenfall AB, to supply fossil-free iron to SSAB’s steel manufacturing facility at Oxelösund, Sweden. Anna Borg, president and CEO of Vattenfall, said that HYBRIT is “a lighthouse initiative”.
The hydrogen will be produced by electrolysing water at Svartöberget Luleå and will be stored in a SEK 250m facility financed equally by the project’s three partners and the Swedish Energy Agency, which provides support via the government’s Industriklivet (Industrial evolution) initiative. Construction began in early 2021, with completion due in summer 2022.
The storage unit is being built using a process called LRC (lined rock cavern), which is a mature technology that has been around for more than 20 years. The rock cavern is of amphibolite with elements of pegmatite and red granite. Most of the elements for the completion of the cavern, ventilation shafts and the pipeline network that will carry the hydrogen around the plant are in place already.
The massive compressor that will pressurise the 100 cubic metre cavern to 250 bar was put in place at the end of 2021, and is being tested to achieve the targeted 100,000–120,000 m3 of hydrogen, enough to power the steel making process for between three to four days.
Many firsts
In June 2021, LKAB delivered the first batch of zero GHG emission iron produced at Luleå to SSAB’s steel mill at Oxelösund, Sweden. Within one month of receipt, SSAB rolled out the first fossil-free steel. It was delivered to their first customer, the Volvo Group, who promptly used it to produce the world’s first-ever vehicle made with fossil-free steel at their construction equipment division based in Braås, Sweden.
The autonomous vehicle will be remembered as the first electric-powered zero-GHG commercial load carrier for use in mining and quarrying, and it was presented to the public on October 13, 2021. Volvo is also planning to design and manufacture a range of trucks with the new fossil-free steel.
On April 1 this year, the HYBRIT partnership was granted €143m by the EU Innovation Fund for demonstrating their GHG-free value chain for producing fossil-free steel.
At the presentation, Frans Timmermans, responsible for the EU’s European Green Deal said: “HYBRIT is paving the way for a fundamental change in the global steel industry. It also demonstrates how fast the green transition can happen: a few years ago, the possibility of producing emission-free steel would have sounded like science fiction. Now, green steel is entering the market”.
Martin Pei, CTO at SSAB said: “Mitigating climate change is of utmost importance and there is no time to lose.”
HYBRIT Development AB, the project’s joint venture company, brought together a group of highly motivated professionals from their respective companies and gave them free rein to design the pathway to a fossil-free steel future. The process has been understood and set up, and will no doubt continue to be developed and refined at SSAB’s pilot plant in Gällivare, next to the LKAB mine.
The pilot should be fully functional by 2025, which will also be when SSAB’s blast furnaces are replaced by electric arc furnaces at Oxelösund, enabling commercial production of fossil-free steel using LKAB’s DRIs by 2026.
Previously, SSAB had been responsible for 10% of Sweden’s, and 7% of Finland’s, CO2 emissions. But once all their steel mills have changed completely over to using the HYBRIT process, it will be 0%. For more information, please visit SSAB’s HYBRIT