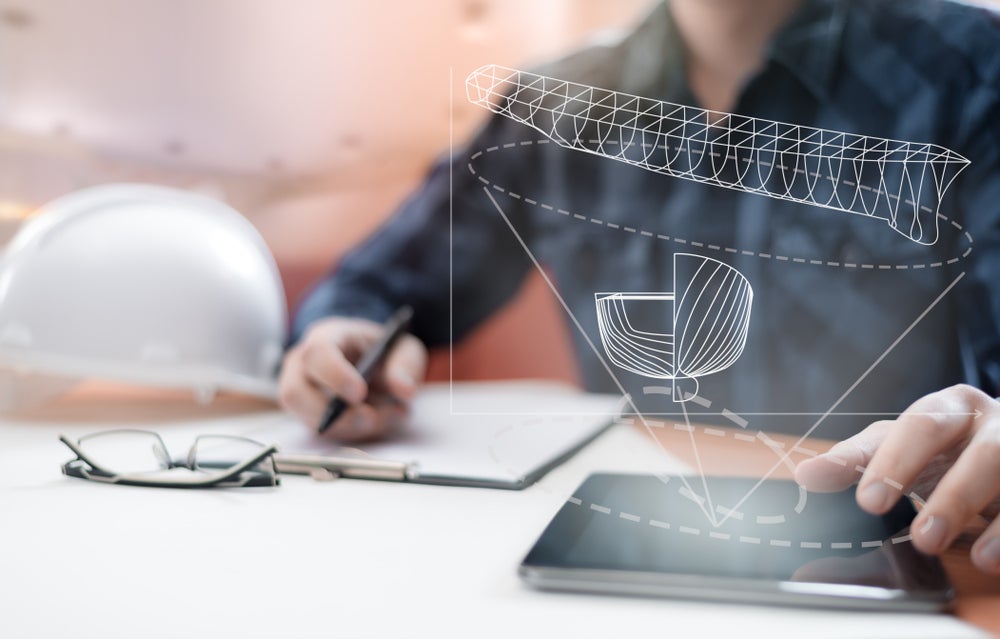
The maritime industry must accelerate innovation and update legacy systems to build operational efficiency in an increasingly digital environment.
Shipbuilding is a highly specialised process that requires a range of technical expertise, often involving multi-year projects. Any changes in regulations, technologies, and customer requirements can extend project timelines and costs. With global supply chains essential to shipbuilding, it is crucial to manage logistics, while coordinating with suppliers and contractors and ensuring quality controls.
The digitalisation of the maritime industry has significant potential to enhance collaboration between contractors and shipyards, improve cost-effectiveness, and provide support in managing the ever-growing volumes of data.
An operations system that manages all marine project data is the first step towards maritime digitalisation. An agile product lifecycle management (PLM) platform can help various global partners in the supply chain access detailed information about every aspect of the shipbuilding process in one centralised system. This can prevent project delays and improve collaboration and efficiency.
Delivering efficient value chains for shipbuilding
Multiple systems such as computer aided engineering (CAE), computer aided design (CAD), computer aided manufacturing (CAM), and product data management (PDM) are frequently utilised in complex shipbuilding projects. These systems are used to design, develop, manufacture, and test the latest ship blueprints. In addition, they generate and store data. However, since separate systems may include contradictory or incomplete information, significant errors can emerge. In most cases, such data can’t be shared with supply chain partners, which may use different tools.
Connecting ship design and engineering systems with PLM software can provide a clear picture of ship data, making it easier to organise and manage, with further enhancements available from the use of artificial intelligence (AI). Through this, improvements can be made with project planning, decreasing errors and redundancies, and boosting overall efficiencies in operations.
An advanced digitalised PLM system can help connect global supply chains and ensure an accurate manufacturing bill-of-materials (MBOM) for procurement planning and decisions. Stakeholders worldwide, from ship owners and operators to repair and maintenance yards, can monitor the functional integration by accessing the complete digital twin model of the vessel stored in the PLM system.
A digital simulation of the ship optimises process flows across the shipyard before production, allowing teams to evaluate performance before investing in physical parts. Through the software, supply chain operations are synchronised, ensuring the right parts are available when they are needed.
However, traditional PLM models rarely provide the versatility to adapt software to a specific project. These issues can be addressed by leading-edge PLM software such as Teamcenter by Siemens, pre-configured for shipbuilding needs. With the ability to combine a range of non-native CAD inputs into a single unified ship structure, Teamcenter is designed to promote co-operation between design teams and operations of various scales. And multinational teams can view it online from any device, reducing accessibility issues.
Optimising IT investments in maritime operations
PLM solutions along with low code capabilities can further enhance marine engineering and design productivity. These solutions allow teams to efficiently design, develop, and deliver sustainable innovations – without programming expertise – while adhering to tight project timelines. Low-code software can also help modernise legacy enterprise software by making it easy to exchange data.
Teamcenter PLM drives innovation in shipbuilding with the Mendix low-code software and out-of-the-box Teamcenter connector. The Teamcenter connector and Mendix connector enables developers to access Teamcenter data and services, allowing further extensions and personalisation specific to marine use-cases.
This integration allows non-technical business users to create apps using pre-packaged tools such as templates, snippets, and widgets. It also includes domain-specific app services such as the 3D viewer app and connectors that permit users to access specific data for use in a workflow.
Siemens Digital Industries Software’s Teamcenter PLM, powered by Mendix low-code software, can accelerate the digitalisation of a shipyard. It empowers team members while democratising app development, by reducing reliance on traditional coding expertise. Low code application development is based on visual, model-driven techniques with a drag-and-drop interface. Users and developers of all skill levels can build apps that enhance existing or upcoming systems with enhanced functionality and interactivity. This reduces backlogs in the IT workflow and provides access to the organisation’s collective knowledge base.
The solution streamlines labour-intensive tasks during shipbuilding, such as planning for every part (PFEP) and an interim inclining test. These processes require collecting and reviewing data from extensive BOM, Teamcenter PLM, 3D renderings, enterprise resource planning (ERP), and more. Traditionally, these tasks would be addressed with conventional coding to tailor the PLM system by in-house IT specialists or third-party software vendors. These processes, while well-established, are neither efficient nor cost-effective.
Instead, the Mendix low-code app Plan for Every Part allows teams to collect data and approvals using automated PFEP. Likewise, inspectors can specify the equipment undergoing 3D rendering for the interim inclining test through the Inclination Test Preparation app while working offline.
Enabling smart shipyards
Modern shipyards gain a competitive advantage with cloud-based technologies to help bridge any knowledge gaps, enabling global design and manufacturing teams to collaborate on projects. With zero upfront capital costs, merging PLM capabilities with a cloud-based platform alleviates the pressure of updating IT systems and storing data on-site.
Through cloud-based PLM technology such as Siemens Teamcenter X, users can securely access and store project information from anywhere, which is crucial for managing shipbuilding project timelines and costs. The innovative software as a service (SaaS) combines the powerful Teamcenter PLM system with an advanced cloud platform, allowing businesses of all sizes to achieve efficiencies while avoiding IT resources previously required for on-premise PLM implementations.
Instant-on PLM enables clients to create a multi-domain bill of materials, providing extensive visibility of the complete digital twin on a cloud platform.
Cloud technology provides unmatched scalability for databases and storage; businesses can expect fast PLM performance despite heavy workloads. It also protects against data loss and security risks courtesy of a secure PLM computing infrastructure.
With features such as pre-configured engineering solutions, predictive AI elements and the option to customise with more SaaS solutions, Teamcenter X can create the smart shipyards required to meet evolving operational challenges.
Discover more about innovative solutions by Siemens Digital Industries Software for the marine industry by downloading the whitepaper below.