Visit our Covid-19 microsite for the latest coronavirus news, analysis and updates
Follow the latest updates of the outbreak on our timeline.
The US Southwest Regional Maintenance Center (SWRMC) has used its capabilities to manufacture face shields for the front-line medical personnel.
The Additive Manufacturing (AM) Team of SWRMC designed and 3D printed face shields for health workers at Naval Medical Center San Diego (NMCSD).
These face shields are used to safeguard staff wearing respirators from the risk of exposure to the virus.
The usability of a mask can be extended by protecting a respirator from the virus, according to SWRMC.
How well do you really know your competitors?
Access the most comprehensive Company Profiles on the market, powered by GlobalData. Save hours of research. Gain competitive edge.
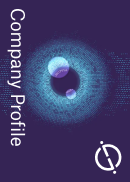
Thank you!
Your download email will arrive shortly
Not ready to buy yet? Download a free sample
We are confident about the unique quality of our Company Profiles. However, we want you to make the most beneficial decision for your business, so we offer a free sample that you can download by submitting the below form
By GlobalDataSWRMC commanding officer captain David Hart said: “SWRMC’s ability to produce 3D printed face shields to aid the medical teams in combating this virus showcases the high velocity learning environment we are part of and the team’s innovative thinking and creativity.
“We are proud of our ability to provide support when the need arises to those on the front lines of this pandemic.”
Work on the face shields commenced in early April.
Following 12-15 man-hours of planning, development and testing, the final product was designed and assembled. It is designed to securely fit staff wearing respirators.
Each face shield frame made using polyethylene terephthalate (PETG) material takes two hours to 3D print.
Using the laser cutter, a clear face shield out of a sheet of plastic can be cut in around 15 seconds.
The masks are produced using in-house materials. So far, the team has produced approximately 85 face shields. It will continue production to meet requirements.